By Derek Peter Clark, founder and co-owner of intra-logistics specialist LOSCYO GmbH, Bielefeld, Germany
An innovative solution for offsite construction puts the building units onto rail-based platforms. The system requires minimal power. The rails are installed flush with the floor and create no barriers on the shopfloor. This enables efficient factory-line production with determined cycle times.

The LOXrail intra-logistics system enables modular building units to be transported through all stages of offsite construction – Image courtesy of ilke Homes, UK
Modular or 3D volumetric construction has triggered a surge in innovation in the construction industry. Improving on conventional prefabrication, which is mostly limited to standardised wall and floor panels, modular construction raises the ratio of works that can be completed in factories to 70% to 90%, depending on the design and the degree of sophistication and individualisation. This makes it an efficient alternative to conventional construction methods, and particularly expedient in light of coinciding deficits in affordable housing, building materials and skilled workers. According to official numbers, 300,000 additional housing units per year will be needed by the mid-2020s. Modular construction provides a reliable way to reduce planning and building time, effort and costs. In addition to individual homes, it is also an attractive solution for housing associations, cooperatives, and municipal developers, allowing them to provide new, high-quality housing in larger quantities within a reasonable timeframe. There are already several big players that specialise exclusively in modular building, covering various sizes from single detached homes to entire blocks of flats, as well as larger buildings for the commercial or public sector such as schools, kindergartens and office blocks.
One-piece flow production of modular homes
As most works are shifted from construction sites to a factory, logistics become of uttermost importance to productivity and efficiency. Following the example of automotive production lines, the spatial separation of individual crafts and construction steps along a production line is most efficient. Thereby, the manufacturing cycle can be clearly structured to run smoothly without collisions and with reliable, transparent material logistics ensuring that the tools and resources for each craft are always on hand when needed. The high proportion of standardised, pre-produced components reduces the need for skilled workers. While the construction of a conventional prefabricated house with onsite assembly of wall and floor panels takes several months, modular homes are completed in a matter of days in such production lines, with transport to the destination and erection also taking only a few days. Moving entire building modules through a factory requires suitable means of transport. The LOXrail system from German manufacturer LOSYCO, originally developed for the manufacturing industries, provides a robust and highly efficient intra-logistics solution for offsite construction. LOXrail tracks and networks can be adapted to individual plant layouts and ergonomically integrated with existing handling solutions such as overhead cranes, lifting platforms, conveyors, automated manipulators or robots.
Low-power ergonomic transport solution
The intra-logistics specialists at LOSYCO have already realised rail-based production lines for modular construction companies in Europe, the UK, the US and Dubai. The low-height transport platforms provide full access from all sides. Workers can step onto them and complete all necessary jobs as they would on the shopfloor. The tracks are laid flush with the floor and thus pose no obstacle for workers, carts or pallet jacks. The hardened steel wheels and round rails are shaped for minimal rolling friction. Bulky and heavy loads can be transported with minimal power, or even pushed by hand. The transport platforms are designed to the particular requirements of the customer. LOSYCO has implemented LOXrail transport solutions for modular housing units measuring up to 40 m² and weighing more than 20 tons. The rails are available in CF53 precision steel or stainless steel with 25 mm or 40 mm diameters for payloads up to 60 tons. The manufacturer offers various customisation options: single tracks or networks including cross-connections between production lines and different ways to power the transport platforms.
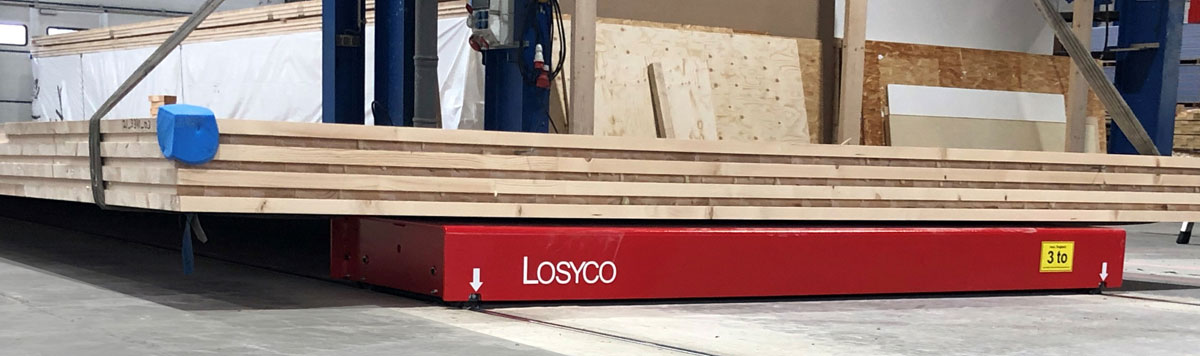
Platforms for manual transport or featuring auxiliary drives are designed to individual requirements – image courtesy of MaxHaus, Germany
Streamlined production
The LOXrail system is an economic, low-maintenance and resilient transport solution that enables modular construction companies to fully utilise the potential of factory-line production. Offsite construction of 3D volumetric units means that almost all construction stages can be completed much more quickly, under repeatable, weather-independent conditions, reducing costs and saving resources and with continuous quality monitoring. Fully equipped modular homes manufactured in one-piece flow production eliminate the need for lengthy planning and elaborate design and coordination work at the construction site, while ensuring consistently high quality standards throughout all production phases. All jobs are seamlessly integrated in an efficient project schedule as almost the entire construction is carried out on the assembly line. Noise and pollution at the building site are also minimised – improving acceptance in the neighbourhoods. Compared to conventional construction methods, offsite construction is much more energy-efficient and environmentally friendly. Modular construction of a typical semi-detached house, for example, can save around 20% more energy and 10% more CO2 per m² than required by the Building Regulations Guidance, Part L1A 2016. In addition, the use of modern construction and insulation materials has a positive effect on the building’s lifetime energy balance: heating costs can be reduced to as little as a third compared to existing solid buildings.
CLICK HERE FOR THE LOSYCO WEBSITE